Below is an excerpt from the 100 years of road safety report from M Sweden.
Riksförbundet M Sweden has worked as the motorists’ consumer organization for over a hundred years. During the time that the organization has existed, the challenges have both changed and been similar. Instead of talking about the road safety problems that arose when the first cars were to be combined with horse-drawn vehicles on the roads, today we talk about the need for center separation and alcobars to reduce accidents. In terms of opinion, our work has swung from, for example, demanding paved roads, to today, among other things, working for better charging infrastructure for electric cars. Basically, it is always about increased road safety, better conditions for motorists and better roads.
iRAP was specifically referenced on page 20 -21 of the report.
Impact of loose gravel on road friction and thus on accident risk
The International Road Assessment Program (IRAP) is a registered global charity whose mission is to save lives worldwide by eliminating road safety hazards. iRAP is active in over a hundred countries and collaborates with governments, road authorities, road user organisations, research institutes and development funds. iRAP conducts extensive research on the relationships between road characteristics and accident risk. The results influence over this decade investments of over USD 100 billion to improve the safety of roads around the world. In addition, reports such as Vaccines for roads, teaching materials and much more are published. The table below from IRAP shows how low road friction affects the risk of different types of road users being involved in a traffic accident. The table shows effect relationships partly for paved roads (sealed), partly for gravel roads (unsealed); see the far-left column.
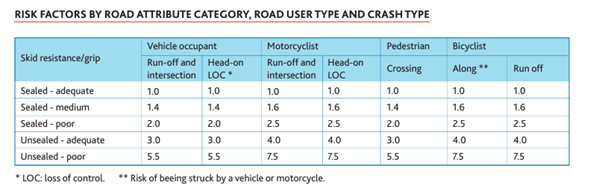
Although the iRAP does not explicitly state metrics for low friction caused by loose gravel on asphalt, there is good reason to believe that such roads fall under the heading Sealed – poor in terms of vehicle grip and handling. The difference between the value 2.0 for Sealed – poor – and the reference 1.0 for Sealed – adequate shows a doubled accident risk. The risk of traffic accidents thus increases dramatically with reduced friction and thus road grip, and with loose gravel on asphalt, friction drops sharply. Develop better requirements for crushed rock material for anti-skid control Stone chip damage to headlights, windscreens, glass sunroofs and paintwork occurs throughout the winter season, with extremely high frequency during the shift from winter to spring during March and April.
More and more motorists drive on unstudded winter tires that polish the road surface shiny and slippery, which together with climate change has led to slippery road conditions occurring more often and thus to increased sanding. Unstudded winter tires are tightly treaded and made from particularly soft rubber compounds, which means that coarse sand and finger grit are more easily stuck in the tire pattern and thrown at other cars. Car manufacturers’ efforts to reduce environmental impact have meant that windshields today are typically ten percent thinner than a decade ago, which has made them more sensitive to stone chips. Due to the fact that EU car regulations are not optimized for driving in cold climates, the previous Swedish requirement for splash guards has also expired. According to an investigation at the research institute Rise, this has almost doubled the number of stone-pelting injuries.
Stone chips occur at meetings, as well as when driving on roads with multiple lanes. Rockfall is particularly common when overtaking and entering acceleration lanes. Stone chips are most common on roads that are mechanically anti-slip by sanding, but also occur on the larger roads that are salted but where the asphalt pavement is of substandard quality. In the past, slip prevention was carried out with uncrushed and therefore cheap natural sand, with its perfectly round grains.
Following political decisions, natural sand quarries and natural gravel quarries have been replaced with fewer and larger rock quarries. This has greatly increased the environmentally burdensome transport work for the winter sand. Anti-slip control is now carried out with different types of rock crusher under names such as stone chips, fine macadam, crushed coarse sand and anti-slip. These “winter sand grains” are more or less flaky, and their shape can make the material quite sharp, with an increased risk of stone chips and other damage.
Today, unfortunately, only these three requirements are typically placed on winter sand for anti-slip:
- Largest grain size approximately 6 millimeters (however, measured on the shortest side of the grains; chipped grains can be significantly longer).
- Cheapest product including delivery to the road operation’s depots.
- The material must not clump together so that it causes blockages in the sand spreaders.
The most effective way to reduce rockfall damage would be to re-allow slip prevention with natural sand. In the absence of natural sand, it remains to set better requirements for winter sand from crushed stone.
In order to create economic, environmentally and sustainable anti-slip control, the following types of requirements for anti-slip winter sand are needed:
- Reduced risk of stone chips by sensibly limiting the chipping of the grains.
- Reduced amount of unhealthy road dust through requirements for the grain’s resistance to being ground down under the heavily loaded and turning steering wheels of city buses.
- Reduced amount of unhealthy road dust by requiring that material with a size of less than about one millimeter be sifted out.
That is to say things like humus from rock exposure, clay and silt from crack filling in the rock mass, as well as crushed fine sand must be sifted out. Such sifted material can instead be advantageously mixed into products for gravel roads, where bonding with the gravel products can create benefit. Such an anti-slip material is classified according to standard SS-EN ISO 14688-1 as a mixture of crushed coarse sand and fine macadam, with grain sizes between one and six millimeters (specified as grading 1/6 mm). Alternatively, only fine macadam graded 2/6 mm is used. There may also be reason to make demands on the grain distribution curve. This should be investigated by, for example, VTI.
iRAP Road Attribute Risk factsheets on the Quality of the Curve is also featured on page 22-23.